The construction industry has historically been slow to adopt new technologies and methods. In recent years, however, modular building solutions have been gaining traction as a viable alternative to traditional construction methods. With the need for sustainability, remote management and cost reduction more important than ever before, modular design is rapidly becoming standard in the industry.
Modular buildings are prefabricated structures built in a controlled environment, then transported to the construction site for assembly. The modular approach offers a range of benefits, including increased efficiency, reduced waste and improved quality control. Here, Hunter’s modular and blast-resistant building experts explore the ways in which modular building solutions are changing the construction landscape for the better.
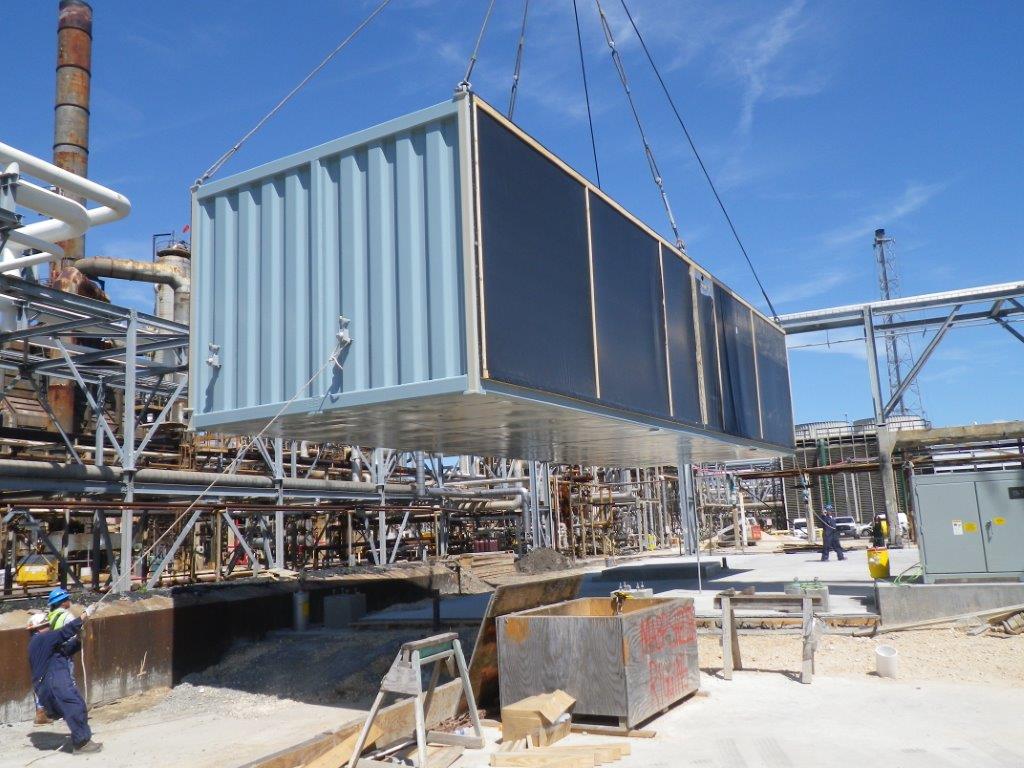
Blast-Resistant Modules Speed Up Construction Projects
While modular construction has been around for decades, recent technological advancements have made it even more efficient. A McKinsey report found that the use of factory-built modules can deliver projects 50% faster than traditional methods. This is because modular buildings are assembled in a controlled factory environment, where inclement weather and other unexpected delays can’t slow down construction. Moreover, the use of computer-aided design and building information modeling make it possible to design and build structures according to exact specifications in a fraction of the time it would take to construct a traditional wood-frame building.
Modular Adoption Drives Industry Standardization
Shortened construction timeframes have not diminished safety standards. On the contrary, as more builders adopt modular solutions enhanced by sophisticated software, the construction industry is becoming safer, less complex and more standardized. Using standard components in a highly controlled factory setting makes it easier to produce structures that meet safety requirements, every time. The approach is equally important for construction crews, who benefit from reduced build time, fewer delays and improved quality control, thanks to the standardization of parts and processes.
Prefabricated Equipment Shelters Cut Costs
Modular building solutions dramatically decrease the overall costs associated with construction projects. Structures assembled offsite are roughly 50% less expensive than traditional builds. And while construction professionals save money on the projects themselves, site setup costs are also shrinking. Prefabricated equipment shelters make it possible to erect high-quality structures that can be reused time and time and again. So rather than investing in temporary shelters only to discard them once a project is complete, modular buildings can simply be moved to the next site.
Modular Construction Supports Sustainability Goals
In addition to increased efficiency and decreased costs, modular buildings make it easier to complete construction projects in a way that reduces waste and protects the environment. Many modular structures are built with energy-efficient materials which can help to limit energy consumption and lower operating costs. Moreover, modules are designed to enter a circular economy of use. Rather than being used once and then discarded, buildings can be assembled, used, disassembled and relocated multiple times, thereby reducing overall consumption and waste. In addition, jobsite deliveries are limited to the transportation of the completed buildings. Instead of coordinating multiple deliveries of unassembled materials, which raises a construction project’s cost and carbon footprint, crews can arrange for fewer shipments of ready-to-use prefabricated modules.
Hunter Highlight: Working with a modular construction firm that can aid in other aspects of a build makes a streamlined process even simpler. Hunter Site Services, for instance, can aid in everything from building installation and replacement services to mechanical work and safety system implementation.
Offsite Construction Simplifies Labor Issues
Many of the issues associated with traditional construction site staffing can be improved upon by modular builds’ factory settings. Modular projects not only require fewer workers overall, but also make it easier to attract and retain skilled laborers drawn to the consistency of reporting to work at a fixed factory location. In factories, workers with specialized skills can move seamlessly from one project to the next, reducing the need for training and eliminating the logistical challenges associated with staffing regularly changing construction sites.
Thanks to their increased efficiency, reduced waste, improved quality control and lower costs, modular building solutions are becoming increasingly popular among a variety of industries. As technology continues to advance, we can expect to see even more innovative solutions in the modular construction space, further transforming the way we approach construction projects.
Are you interested in exploring modular building solutions? At Hunter, we take time to learn the unique needs of your project, then partner with you to deliver a finished product that serves you on every front. Contact the Hunter team to learn more about how modular construction can decrease costs, speed project completion and increase safety. Our modular and blast-resistant building experts would love to hear from you and can facilitate work around the globe.